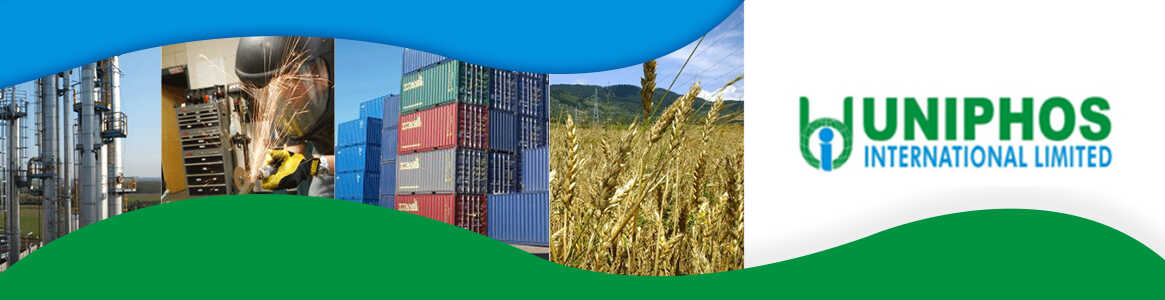
Uniphos International Ltd - | E-Showroom
Uniphos International Ltd - | E-Showroom
The majority of sulphur that is transported around the world is done as a bulk solid. The sulphur is often stored in the open in huge stockpiles at terminals ready to be loaded onto ships, railcars or truck or at plant sites to be melted and used in the production of sulphuric acid. Most sulphur stockpiles are located outdoors in open where it is exposed to wind, rain, dust, salt air, etc. In some cases sulphur is stored indoors where some protection from the elements is available.
Bulk sulphur produced from sulphur that has been crushed from larger pieces will be irregular in shape and posses many sharp edges and points which will be easily broken producing smaller particles and dust.
The properties of solid elemental sulphur leave a lot to be desired from the point of view of handling and transport. Since it is by no means always Practical to move sulphur around in the molten form, the sulphur industry has expended a considerable amount of effort over the years on developing methods of forming sulphur into regularly-sized particles which can be handled without giving rise to excessive amounts of dust.
Liquid/Molten SulphurMolten sulphur is present in an ever widening presence in many industries. Besides the traditional sources of sulphur, such as refineries and natural gas plants, and the well known users of sulphur, such as sulphuric acid plants and fertilizer production, sulphur has become a common feedstock in more conventional chemical production such as tire and rubber additives, polymer production, and even food products.
sulphur is transported both as a solid in bulk and as a liquid in the molten form. Each form has its own special requirements in order to transport sulphur safely, with minimal environmental impact and minimal contamination of the sulphur.
The key to transporting sulphur in molten form is maintaining its temperature at approximately 140oC. Transport over short distances can be done in well insulated containers. The low thermal conductivity of sulphur minimizes heat loss and helps it to retain heat so it does not solidify. Over longer distances, a heating system is required to maintain the sulphur in the liquid state.
Tank trailers designed for molten sulphur are generally dedicated to hauling molten sulphur. A tank that has just carried molten sulphur cannot be easily cleaned so that the trailer can carry a different commodity on the return trip or to another destination. The result is that the tank is full on the delivery trip but is empty on the return trip. To maximize what is known as \"loaded miles\", a specially designed tank trailer combines a tank for molten sulphur and a bulk carrier. On one trip, the trailer carries molten sulphur and on the return trip carries a bulk commodity such as fertilizers. This type of trailer is called a backhaul double and is used in the Florida region by fertilizer manufacturers to improve the trucking economics. Backhaul doubles are also used in western Canada but instead of a sulphur/bulk carrier, a sulphur/fuel carrier is used.
sulphur can be shipped in either solid or liquid form over long distances by ocean going ships. Solid sulphur can be shipped in virtually any bulk carrier provided care has been taken to thoroughly cleanout the hold. Molten sulphur is transported in specially designed ships equipped with heating systems.
Slated SulphurSlate sulphur is formed by pouring molten sulphur on a moving belt where it is solidified into a continuous slab with a thickness of 3 to 5 mm. The sulphur begins to break into smaller pieces when it is separated from the belt and when sulphur is discharged from the belt at the head pulley. This process produces irregular shaped pieces with sharp edges. Fines (less than 50 Tyler Mesh) amount to about 3.5% by weight. Additional fines are produced through further handling of the product.
Slating Process was developed to meet the need for a low cost, high volume method of converting molten sulphur into a solid form that can be stockpiled and handled using conventional bulk handling techniques.
The slating technology uses a liquid sulphur spread pan to apply molten sulphur evenly to a slow moving slating belt, on which the molten sulphur is cooled and subsequently solidifies to a solid sheet.
Cooling is accomplished through both air-cooling and immersion in water as the belt transports the sulphur to the discharge point at the head pulley of the slating unit.
Molded SulphurA refined sulphur molded into half cylinder shaped bricks averaging 0.75 to 1.5 pounds each. This product is primarily used in oil refining, steel production, and secondary smelting.
Prilled SulphurIn the wet sulphur prilling process, molten sulphur is pumped on to perforated trays that direct the sulphur in narrow streams into an agitated water bath. Pellets form as the sulphur comes in contact with the water. The low thermal conductivity, high specific heat, and long transformation time of sulphur make it necessary to maintain the pellets in suspension for as long as possible, allowing them to harden. This process produces spherical, uniformly sized, low moisture pellets.
The wet process forms prills by pumping liquid sulphur onto perforated trays through which the sulphur streams into an agitated water bath. As the molten sulphur streams contact the cool water, the pellets form and are maintained in suspension to allow enough time to solidify.
The solid prills settle to the bottom of the prill tank and flow by gravity to high frequency dewatering screens. The cooling water and undersized prills recovered from the dewatering screens flow by gravity to a settling tank where undersize prills are removed from the settling tank using a screw conveyor. The undersize prills can then be remelted or blended with the final product on the collector conveyor.
The process water is pumped back to the prill tank by water pumps mounted on the settling tank, passing through a water cooled heat exchanger that removes the heat delivered to the process by the liquid sulphur. As the process water is contained in a closed loop system, makeup water to compensate for losses due to evaporation and product water is minimal.
sulphur prills of product quality are discharged to a belt conveyor for transport to storage and/or further handling.
Pastillated SulphurPastillated process is a drop-forming technology, solidifying liquid sulphur into uniform hemispherical pastilles. The technology uses a rotary depositor mounted above, and transversely to, a metal cooling belt. The depositor consists of a perforated rotating shell with an internal distribution and metering bar, which produces closely spaced rows of precisely metered drops.
Molten sulphur product at approximately 125oC is continuously fed through heated pipes at the specified pressure to the dropforming depositor. The rotational speed of the shell is synchronized with speed of the cooling belt to ensure that the droplets assume a hemispherical shape upon contact with the belt.
Owing to conductive and convection cooling processes, solidification of the droplets begins at the surface, thereby preserving the hemispherical shape, and progresses into the centre. A small dimple forms at the top of the pastille during the solidification process to accommodate volumetric shrinkage.
The temperature of the cooling belt is controlled by regulating the flow and temperature of the cooling water sprayed onto the underside of the belt. The cooling water is collected and re-circulated through a cooling system. Control of the heat transfer rate from the molten sulphur droplets to the metal belt and from the metal belt to the cooling water not only optimizes production capacity, but also ensures the production of a high quality product.
A release agent is applied to the metal cooling belt to ensure trouble free product discharge and to aid in forming proper pastille shape. The solid pastilles discharge from the forming unit at about 70oC and are ready for storage or packaging.
Granulated SulphurIn response to the need for a new generation of formed sulphur to meet the increasingly stringent standards imposed in the late 70s by both environmental considerations and customer preference,sulphur formig leaders developed and successfully commercialized a sulphur forming process known as the granulation process.
The granulation process uses a size enlargement process to transform molten sulphur into dense spherical solid granules. Small particles of sulphur (seed) are introduced at the feed end of the drum and are sprayed and coated with molten sulphur as the product moves toward the drum discharge. Each applied layer is cooled to solidification before another coat of molten sulphur is applied. With repeated application, bonding and then cooling of successive coats, the seeds increase in volume and weight until they reach the desired granule size, usually 1 to 6 mm in diameter. A screening process separates undersize granules from the product size granules, which allows the undersize to be recycled to the drum inlet as seeds.